Herr Beisel, Sie haben erlebt, wie in Mannheim vor dreißig Jahren der einmillionste Traktor produziert wurde und nun vor kurzem auch der zweimillionste. Was hat sich in dieser Zeit alles getan?
Die erste offensichtliche Veränderung, die mir in den Kopf kommt, ist die gestiegene Komplexität der Traktoren. Anfangs konnte man noch von einem Ende des neuen Montagebandes zum anderen schauen. Heute stehen überall Kisten am Band und von der Decke hängen irgendwelche Werkzeuge und Geräte. Das sieht komplett anders aus, das sind zwei Welten. Vor 30 Jahren war an dem Traktor fast keine Elektronik dran. Da gab es eine mechanische Einspritzpumpe und wenn die nicht gelaufen ist, dann musste man klassischerweise den Gaszug richten und alles lief wieder.

In den 2000ern wurde der Traktor dann komplett ich sage immer verelektrifiziert. Wir kamen dann mit einer elektronischen Einspritzung. Das Gaspedal war auf einmal ein kleines Potentiometer, der eingebaut werden musste. Dann kam die gefederte Vorderachse und wo es früher zwei bis drei Steuergeräte gab, gibt es heute 6 oder sogar 8. Hinzu kamen all die elektronischen Steuerelemente, im größten Modell befinden sich heute 14 oder sogar 16 Controller. Wegen der hohen technischen Komplexität und Variantenvielfalt sind viele Arbeitsschritte heute direkt am Hauptmontageband gar nicht mehr möglich und müssen ausgelagert werden.
Gibt es ein konkretes Beispiel aus ihrer persönlichen Arbeit, welches das Ausmaß der Veränderungen zeigt?
Ein gutes Beispiel ist die Vormontage der Motorhauben. Das war nach Abschluss meiner Ausbildung zum Industriemechaniker im Jahr 1992 eine meiner ersten Aufgaben. So eine Haube bestand zu dieser Zeit komplett aus Blech, also ohne Kunststoffteile. Ich montierte insgesamt etwa 30 Teile: dort das Scharnier, hier zwei Schrauben, dann noch einen Schweinwerfer-Grill mit zwei Schweinwerfern, die Gummidichtung und ein bisschen Gestänge – fertig war der Job.
Wenn ich mir da im Vergleich heute die Hauben unserer größeren Traktoren anschaue – da sind allein 250 Schrauben drin. Auch die Variantenvielfalt hat zugenommen. Früher gab es die Wahl zwischen zwei Konfigurationen für die Beleuchtung, einem für den Rechtsverkehr, einem für den Linksverkehr. Heute haben wir Low Beams, High Beams, LEDs, nicht LEDs und das alles für den Rechts- und Linksverkehr. Da hat sich schon einiges getan. Auch die Arbeitsinhalte wurden immer weiter optimiert und verdichtet.

Wie schaffen Sie es, diese Komplexität im Werk zu beherrschen?
Step by Step haben wir uns da herangearbeitet. Ein großes Plus unseres Werks ist, dass wir sehr viele Mitarbeitende haben, die schon sehr lange bei uns arbeiten. So ist die Belegschaft mit dem Werk gewachsen und kann bei jeder Herausforderung ihre ganze Erfahrung einbringen. Sie haben die Komplexität mit der Zeit gelernt, ohne es wirklich zu bemerken. Außerdem haben wir in der Fertigung heute viel automatisierte Unterstützung und es arbeiten in den Teams pro Gruppe mehr Menschen als früher. Das ist nötig, um die Aufträge, die wir haben, so zügig und zuverlässig zu erfüllen, wie wir das tun.
Welche Rolle spielt die Automatisierung?
Wir haben hier in Mannheim mittlerweile viele Bereiche, die extrem automatisiert sind. Gerade in der Teilefertigung arbeiten Roboter, die etwa Fräs- oder Drehmaschinen automatisiert bestücken. Auch in der Endmontage ist mehr automatisiert: Früher haben wir den Rahmen von Hand in Vorrichtungen zusammengeschraubt. Heute haben wir einen Roboter in der Schraubstation.
So bekommen wir Mitarbeiter immer mehr Unterstützung, was natürlich auch die Ergonomie verbessert. Wichtig ist mir bei diesem Thema: Die Automatisierung soll eine Entlastung sein, also immer im Sinne der Mitarbeiter erfolgen. Sie tragen das ganze Know-How in sich und mit ihnen möchte ich auch in Zukunft arbeiten.
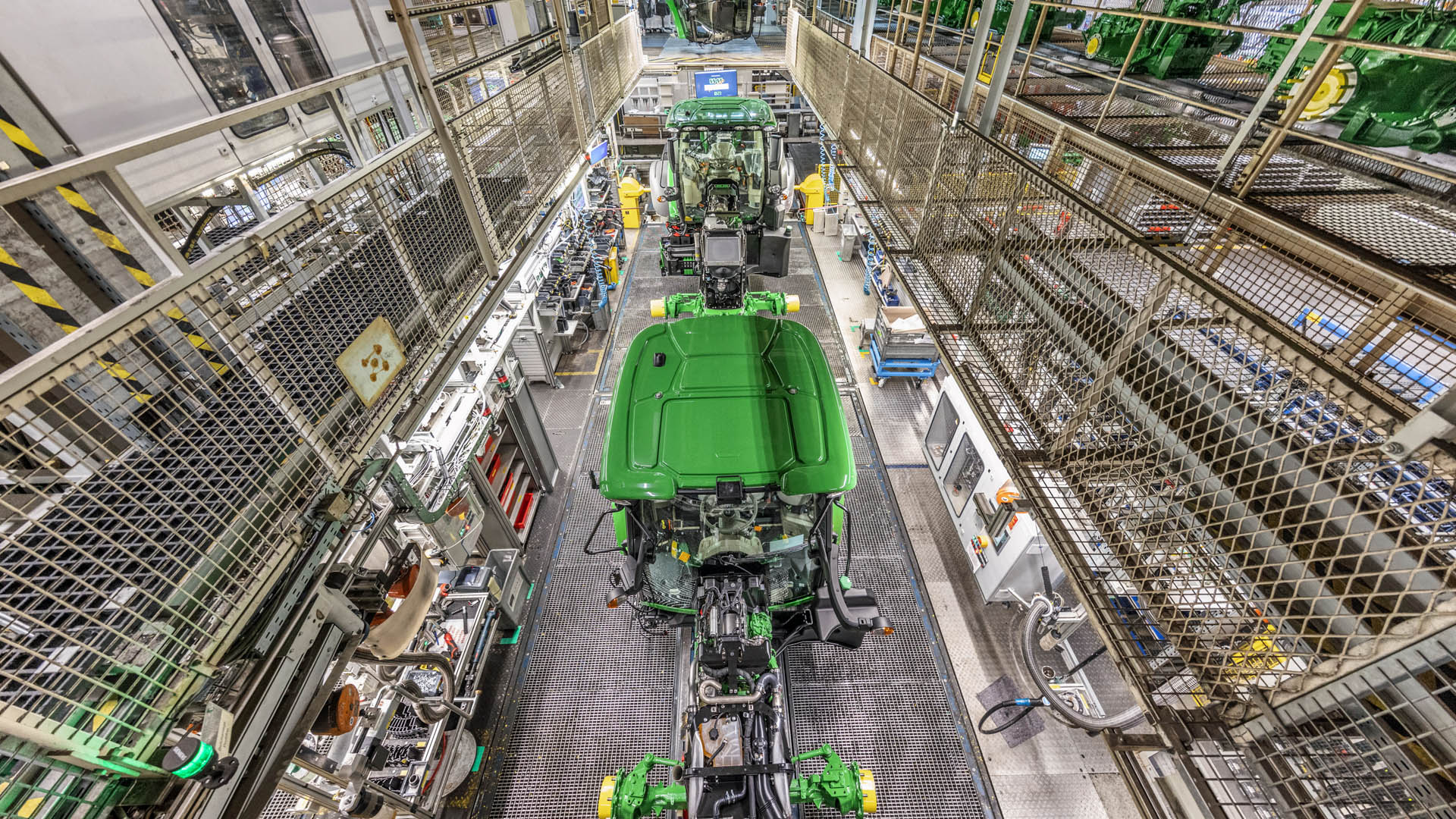
Was waren für Sie persönlich die größten Highlights im Lauf der Jahrzehnte?
Toll fand ich, als man das Werk für Besucher geöffnet hat. Das gab es so früher gar nicht. Das war eine schöne Entwicklung, dass wir da nach außen hin offener geworden sind. Ich bin in der unmittelbaren Nachbarschaft des Werks aufgewachsen und habe bis kurz vor Beginn meiner Ausbildung gar nicht gewusst, was hinter den roten Backsteinmauern passiert. Heute kennen die Leute aus der Umgebung das Unternehmen deutlich besser und wissen sofort etwas mit dem Namen anzufangen, wenn ich erzähle, dass ich bei John Deere arbeite.
Ein Highlight war sicher auch, wie wir damit umgegangen sind, als es einmal Probleme mit der Lieferung der Reifen gab. Wir konnten es uns nicht leisten, keine Traktoren zu bauen, bis Reifen wieder zuverlässig geliefert werden. Also sagten wir uns: „Wir können auch Traktoren ohne Reifen bauen.“ Und so bauten wir 800 Schlepper ohne Reifen, die dann erst nachträglich bereift wurden. Das ermöglichte es uns, die Produktion trotz Lieferengpass nicht still stehen zu lassen. Unser Motto ist: Geht nicht, gibt’s nicht.

Wie würden Sie Ihre 35 Jahre bei John Deere zusammenfassen?
Insgesamt kann ich sagen: Bei John Deere konnte ich vom Auszubildenden zur Führungskraft wachsen und habe in der gleichen Zeit das Werk wachsen sehen. Das ist ein gutes Gefühl.